Fotorezistin kaplama yöntemleri genellikle döndürerek kaplama, daldırmalı kaplama ve rulo kaplamaya ayrılır; bunların arasında döndürerek kaplama en yaygın olarak kullanılır. Döndürerek kaplama yoluyla, fotorezist alt tabaka üzerine damlatılır ve alt tabaka, bir fotodirenç filmi elde etmek için yüksek hızda döndürülebilir. Bundan sonra sıcak bir plaka üzerinde ısıtılarak katı bir film elde edilebilir. Döndürerek kaplama, ultra ince filmlerden (yaklaşık 20 nm) yaklaşık 100 um'lik kalın filmlere kadar kaplama için uygundur. Özellikleri iyi bir tekdüzelik, levhalar arasında tekdüze film kalınlığı, az kusur vb.'dir ve yüksek kaplama performansına sahip bir film elde edilebilir.
Döndürerek kaplama işlemi
Döndürerek kaplama sırasında alt tabakanın ana dönüş hızı, fotorezistin film kalınlığını belirler. Dönme hızı ile film kalınlığı arasındaki ilişki aşağıdaki gibidir:
Döndürme=kTn
Formülde Spin dönüş hızıdır; T film kalınlığıdır; k ve n sabitlerdir.
Döndürerek kaplama işlemini etkileyen faktörler
Film kalınlığı ana dönüş hızına göre belirlense de aynı zamanda oda sıcaklığı, nem, fotorezist viskozitesi ve fotorezist tipi ile de ilgilidir. Farklı fotorezist kaplama eğrilerinin karşılaştırılması Şekil 1'de gösterilmektedir.
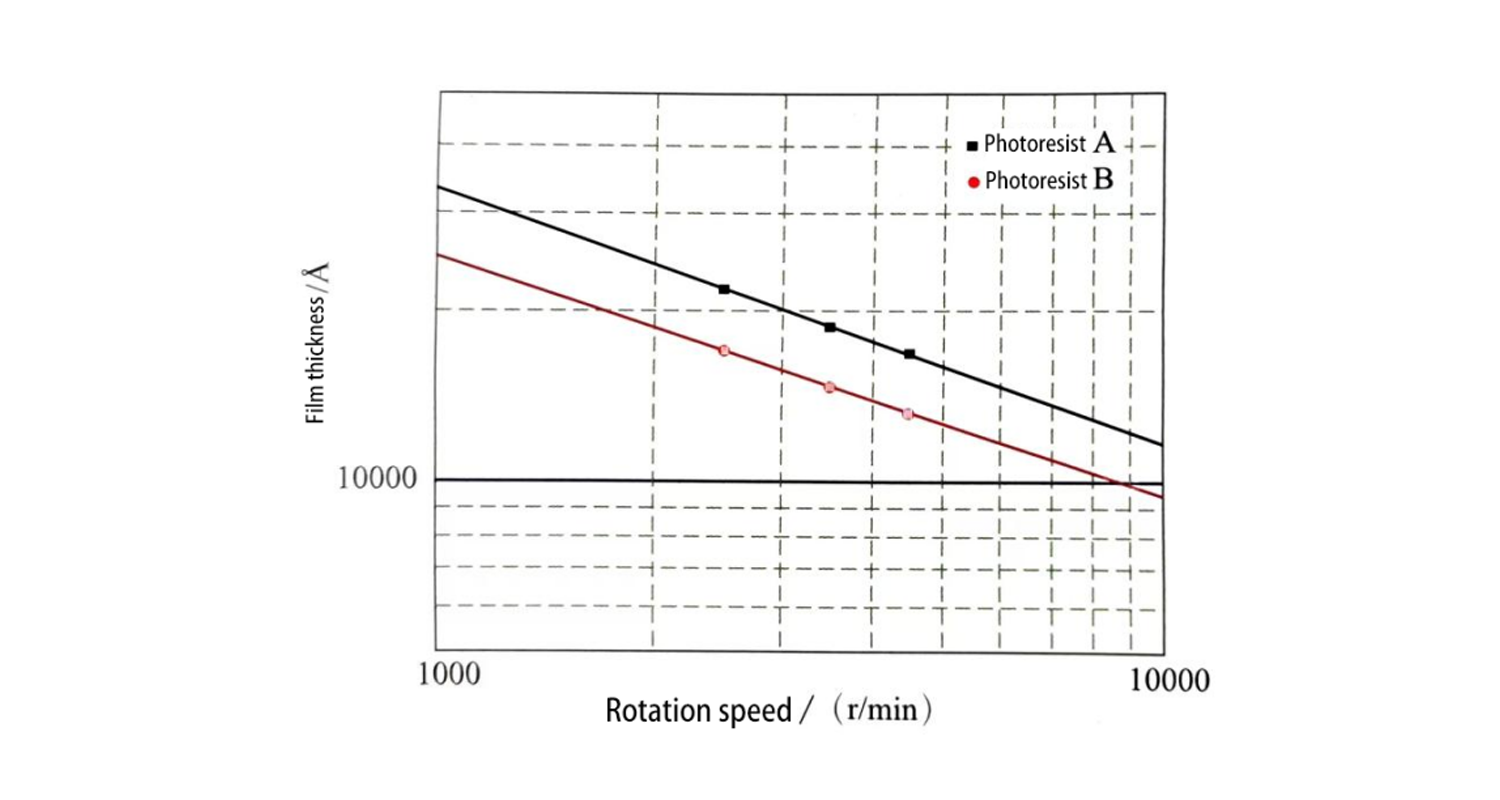
Şekil 1: Farklı türdeki fotorezist kaplama eğrilerinin karşılaştırılması
Ana dönüş süresinin etkisi
Ana dönüş süresi ne kadar kısa olursa film kalınlığı da o kadar kalın olur. Ana dönüş süresi arttığında film o kadar incelir. 20 saniyeyi aştığında film kalınlığı hemen hemen değişmeden kalır. Bu nedenle ana dönüş süresi genellikle 20 saniyeden fazla olacak şekilde seçilir. Ana dönüş süresi ile film kalınlığı arasındaki ilişki Şekil 2'de gösterilmektedir.
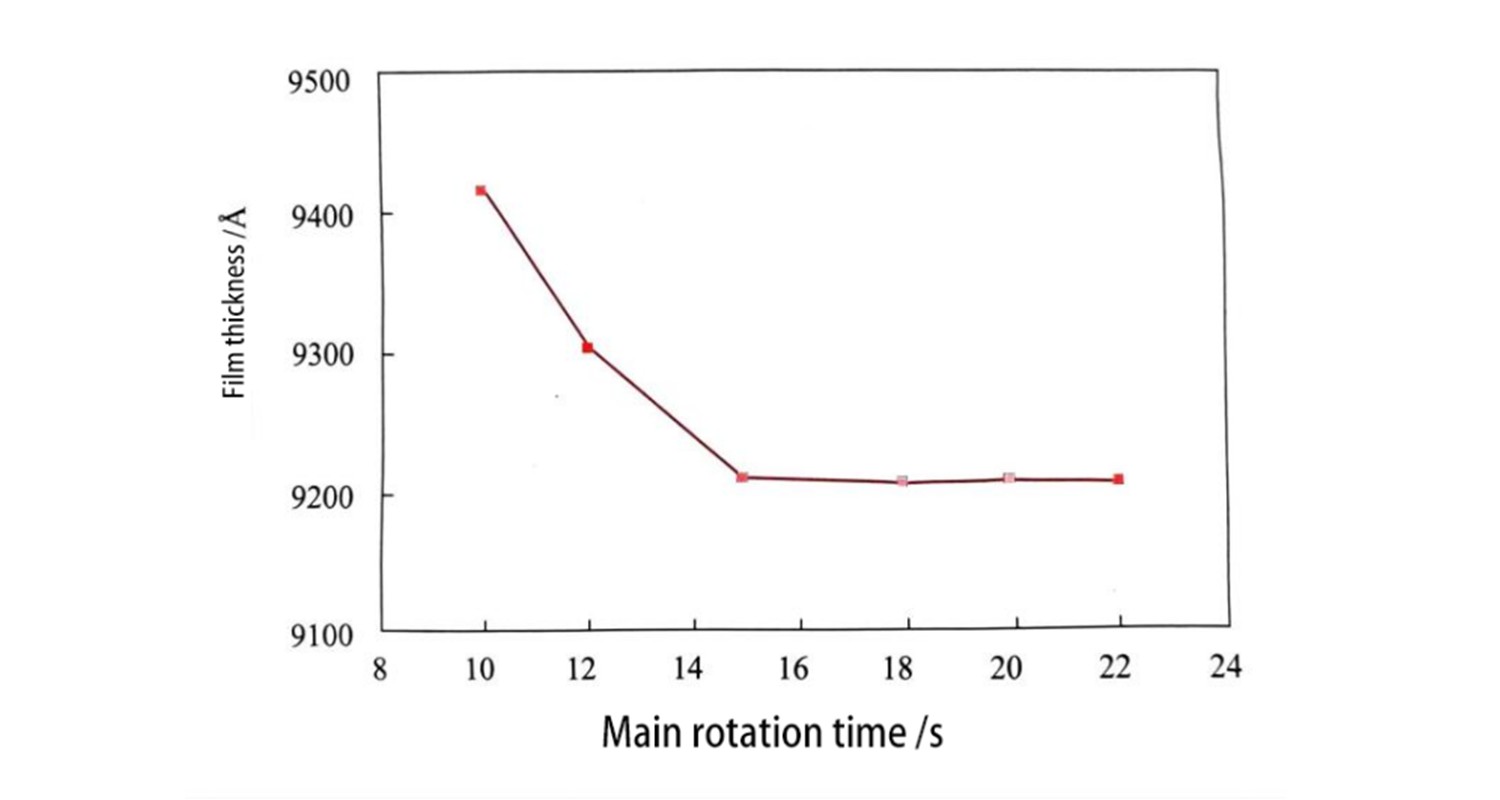
Şekil 2: Ana dönüş süresi ile film kalınlığı arasındaki ilişki
Fotorezist alt tabaka üzerine damlatıldığında, sonraki ana dönüş hızı aynı olsa bile, damlama sırasında alt tabakanın dönüş hızı son film kalınlığını etkileyecektir. Fotorezist filmin kalınlığı, damlama sırasında alt tabaka dönüş hızının artmasıyla artar; bu, damlama sonrasında fotorezist açıldığında solvent buharlaşmasının etkisinden kaynaklanmaktadır. Şekil 3, fotorezist damlaması sırasında farklı alt tabaka dönüş hızlarında film kalınlığı ile ana dönüş hızı arasındaki ilişkiyi göstermektedir. Damlayan alt tabakanın dönüş hızının artmasıyla film kalınlığının daha hızlı değiştiği, ana dönüş hızının düşük olduğu bölgede farkın daha belirgin olduğu şekilden görülmektedir.
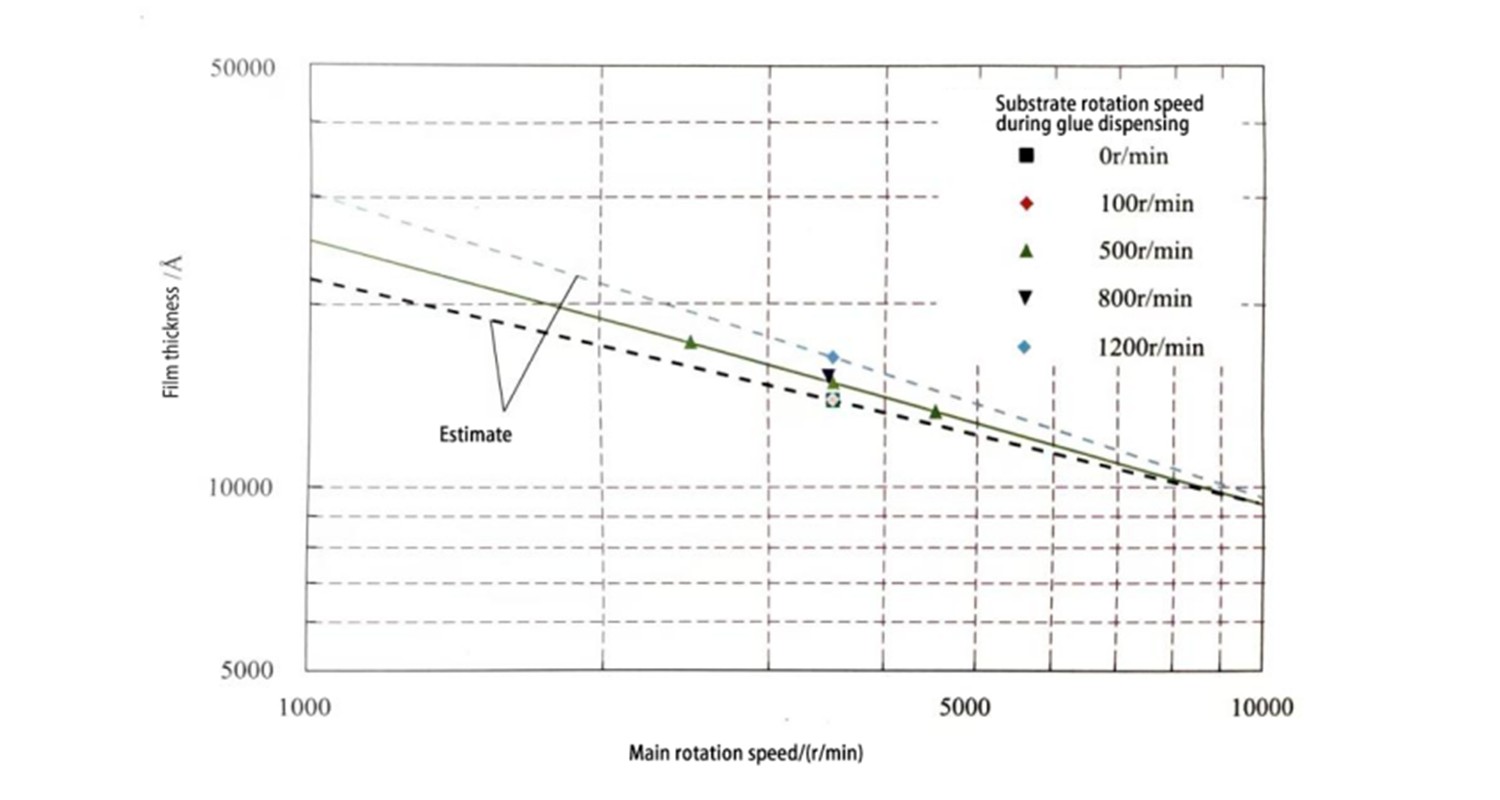
Şekil 3: Fotorezistin dağıtılması sırasında farklı alt tabaka dönüş hızlarında film kalınlığı ile ana dönüş hızı arasındaki ilişki
Kaplama sırasında nemin etkisi
Nem azaldığında film kalınlığı artar çünkü nemdeki azalma solventin buharlaşmasını hızlandırır. Ancak film kalınlığı dağılımı önemli ölçüde değişmez. Şekil 4'te kaplama sırasında nem ile film kalınlığı dağılımı arasındaki ilişki gösterilmektedir.
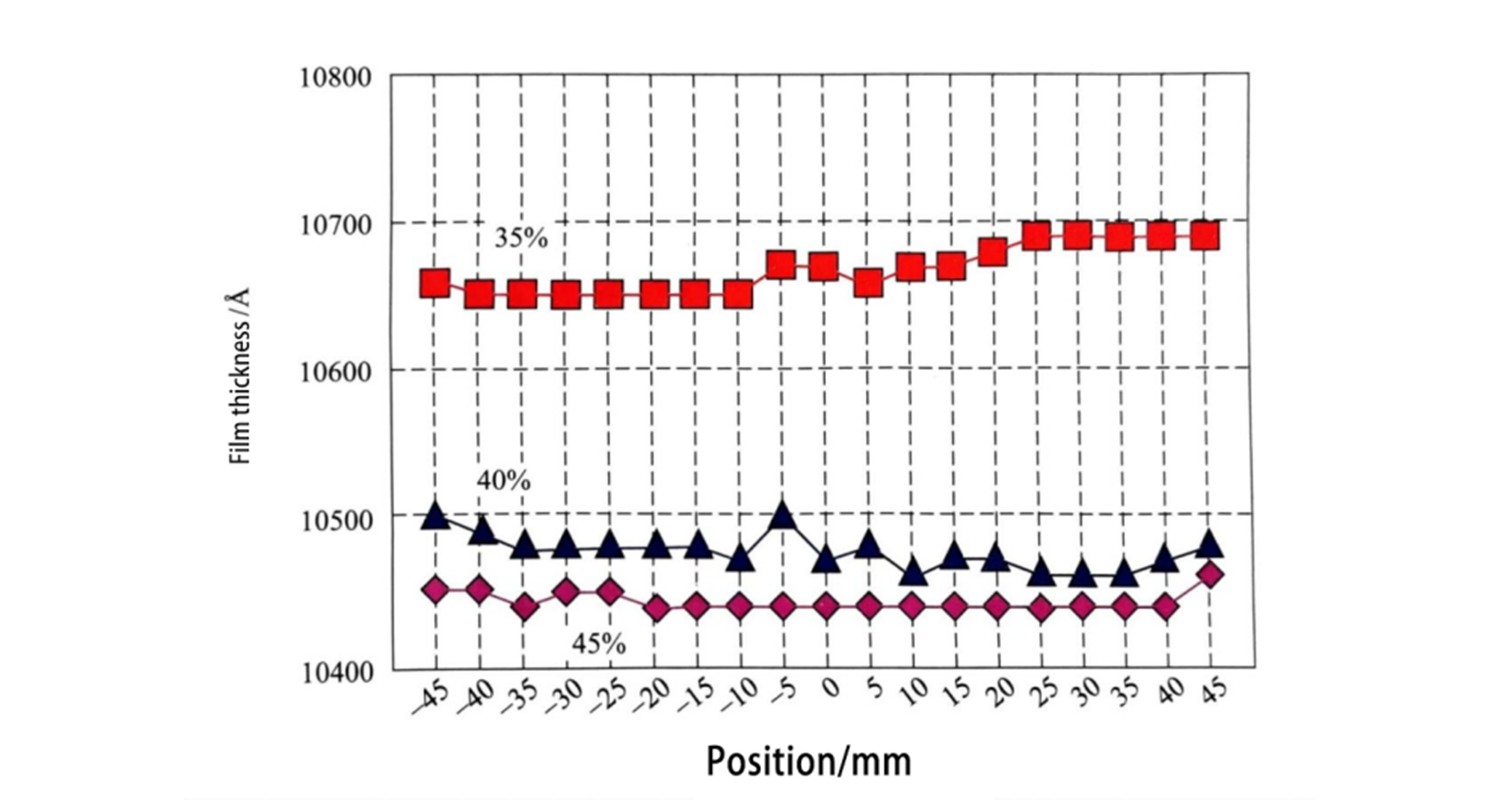
Şekil 4: Kaplama sırasında nem ve film kalınlığı dağılımı arasındaki ilişki
Kaplama sırasında sıcaklığın etkisi
İç ortam sıcaklığı arttığında film kalınlığı artar. Şekil 5'te fotorezist film kalınlığı dağılımının dışbükeyden içbükeyliğe doğru değiştiği görülmektedir. Şekildeki eğri aynı zamanda en yüksek homojenliğin iç ortam sıcaklığı 26°C ve fotorezist sıcaklığı 21°C olduğunda elde edildiğini göstermektedir.
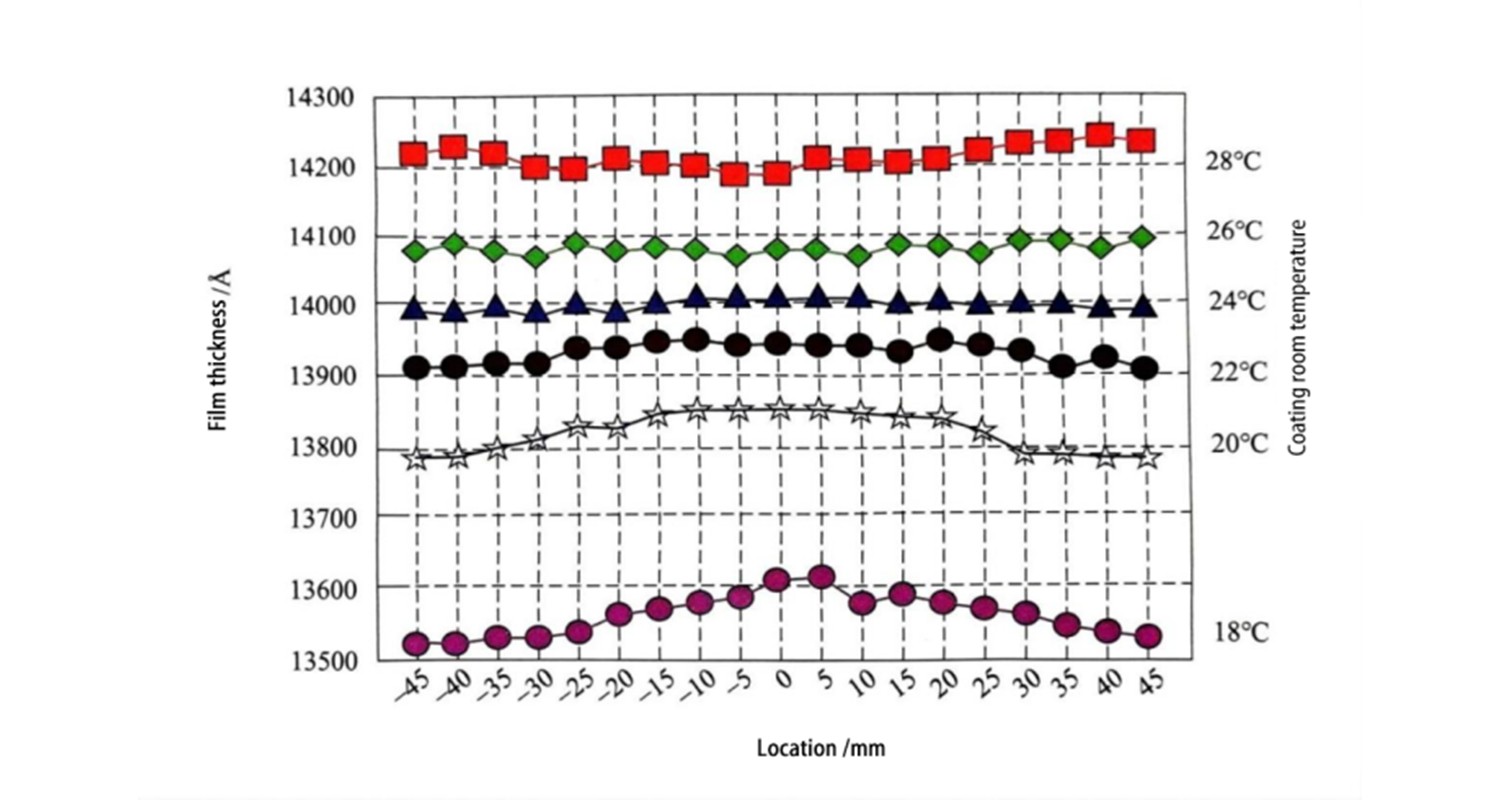
Şekil 5: Kaplama sırasında sıcaklık ile film kalınlığı dağılımı arasındaki ilişki
Kaplama sırasında egzoz hızının etkisi
Şekil 6 egzoz hızı ile film kalınlığı dağılımı arasındaki ilişkiyi göstermektedir. Egzozun yokluğunda bu, levhanın merkezinin kalınlaşma eğiliminde olduğunu gösterir. Egzoz hızının arttırılması üniformiteyi artıracaktır ancak çok fazla arttırılırsa üniformite azalacaktır. Egzoz hızı için optimal bir değerin olduğu görülebilir.
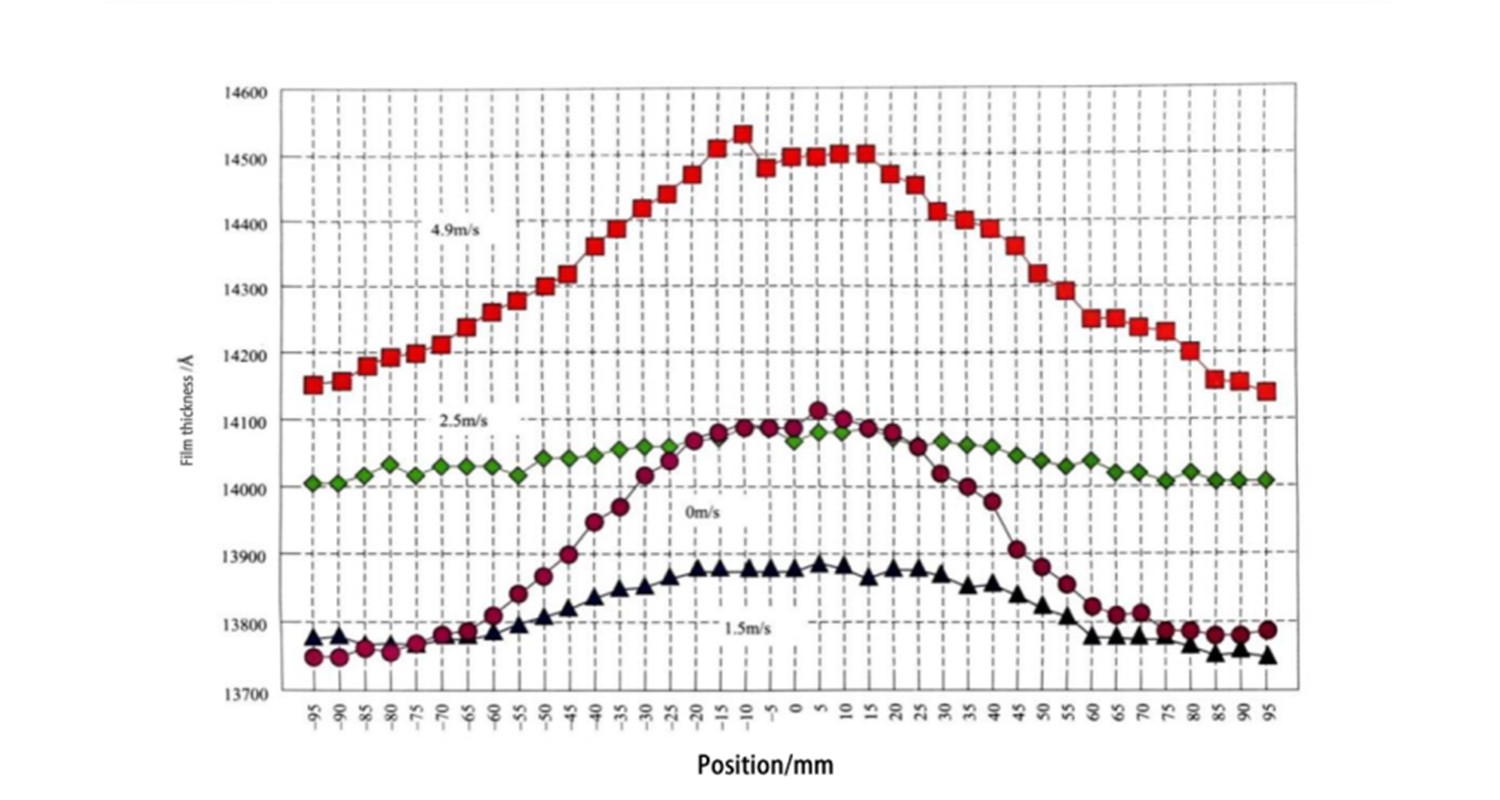
Şekil 6: Egzoz hızı ile film kalınlığı dağılımı arasındaki ilişki
HMDS tedavisi
Fotorezisti daha kaplanabilir hale getirmek için levhanın heksametildisilazan (HMDS) ile işlenmesi gerekir. Özellikle Si oksit filmin yüzeyine nem bağlandığında silanol oluşur ve bu da fotorezistin yapışmasını azaltır. Nemi uzaklaştırmak ve silanolü ayrıştırmak için, levha genellikle 100-120°C'ye ısıtılır ve kimyasal bir reaksiyona neden olmak için HMDS sisi eklenir. Reaksiyon mekanizması Şekil 7'de gösterilmektedir. HMDS işlemi sayesinde küçük temas açısına sahip hidrofilik yüzey, büyük temas açısına sahip hidrofobik bir yüzeye dönüşür. Gofretin ısıtılması daha yüksek fotodirenç yapışması elde edebilir.
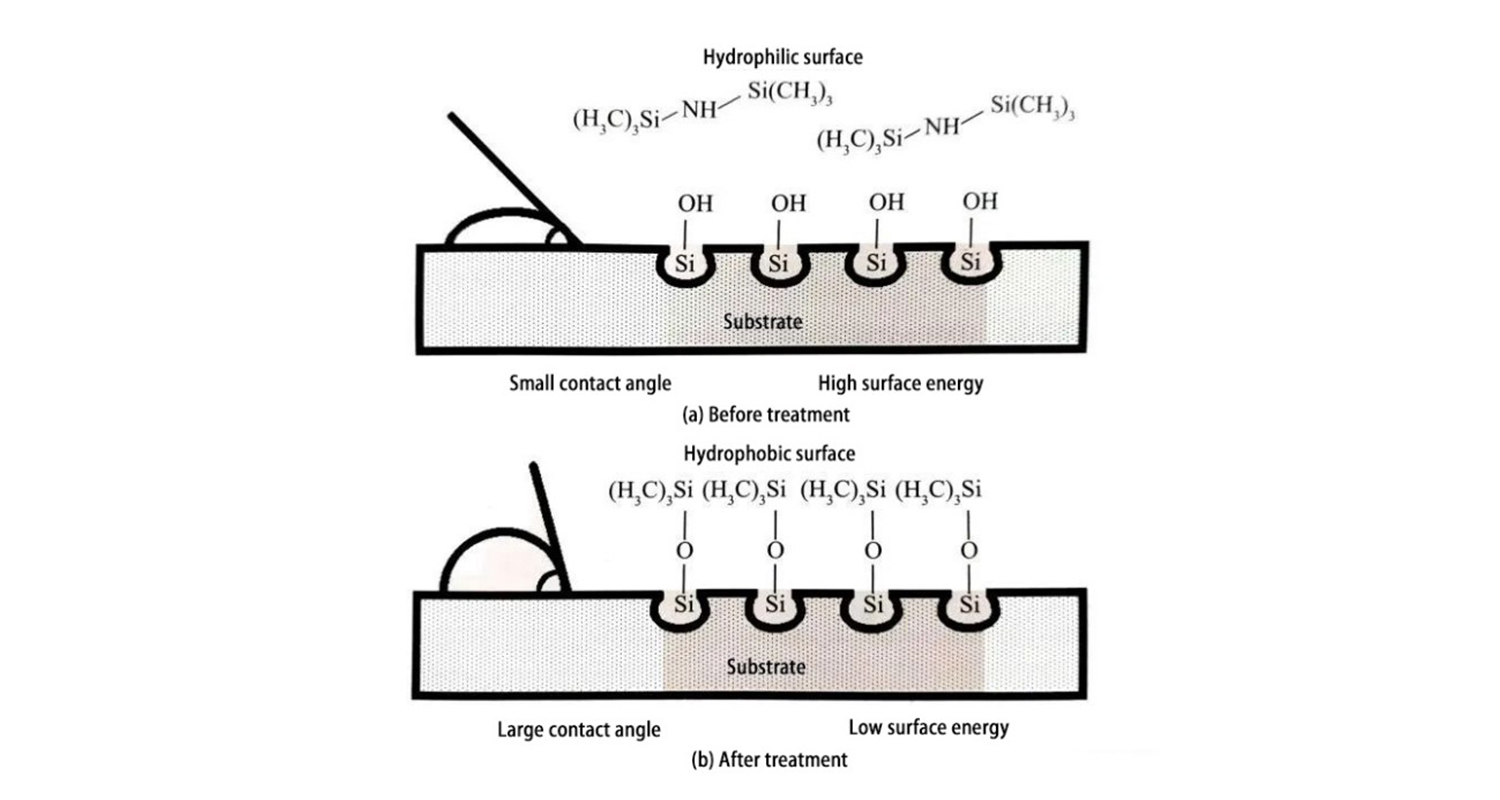
Şekil 7: HMDS reaksiyon mekanizması
HMDS tedavisinin etkisi temas açısı ölçülerek gözlemlenebilir. Şekil 8, HMDS tedavi süresi ile temas açısı (tedavi sıcaklığı 110°C) arasındaki ilişkiyi göstermektedir. Substrat Si'dir, HMDS tedavi süresi 1 dakikadan fazladır, temas açısı 80°'den büyüktür ve tedavi etkisi stabildir. Şekil 9, HMDS işlem sıcaklığı ile temas açısı (tedavi süresi 60 saniye) arasındaki ilişkiyi göstermektedir. Sıcaklık 120°C'yi aştığında temas açısı azalır, bu da HMDS'nin ısı nedeniyle ayrıştığını gösterir. Bu nedenle HMDS tedavisi genellikle 100-110°C'de gerçekleştirilir.
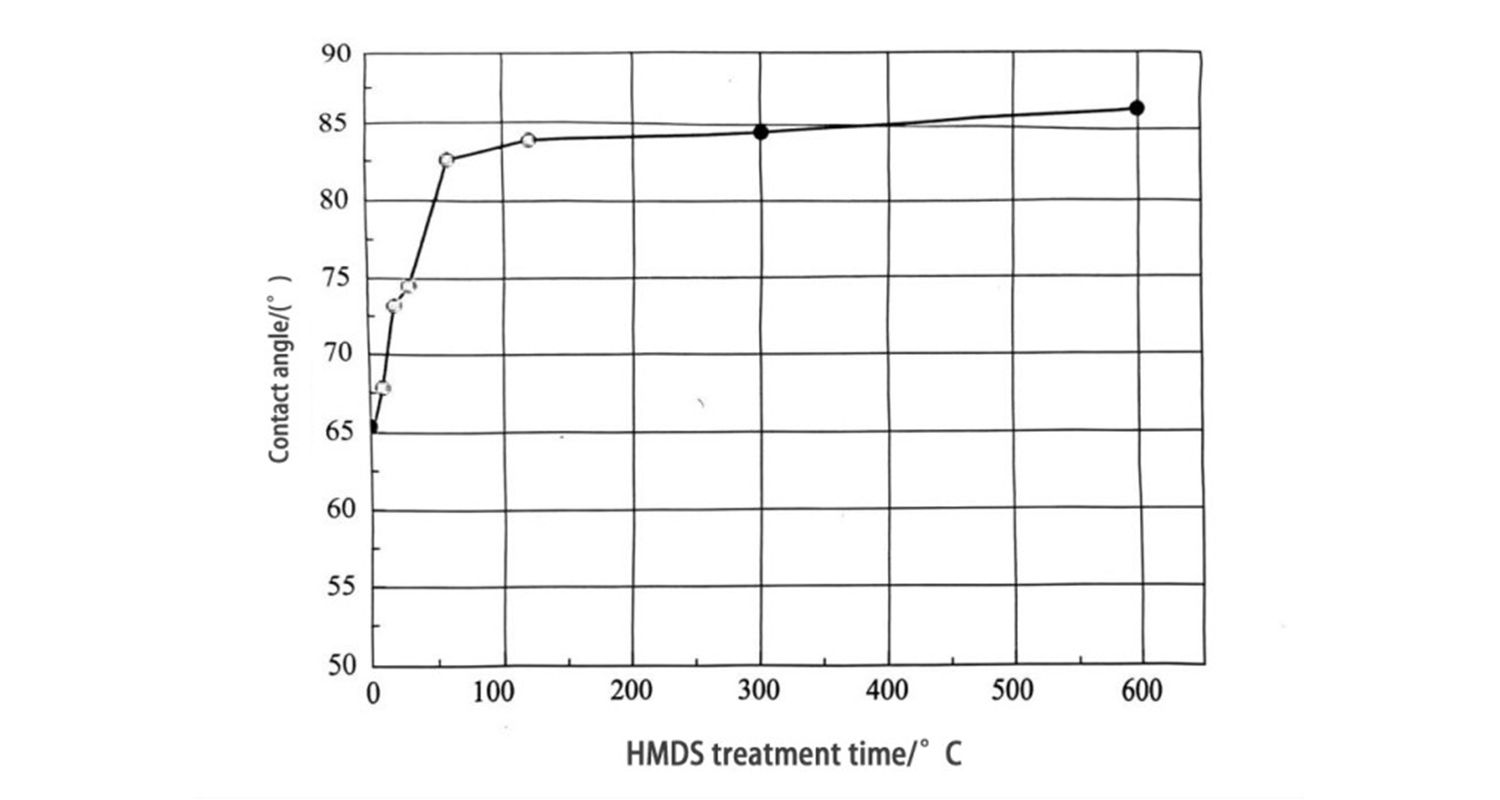
Şekil 8: HMDS tedavi süresi arasındaki ilişki
ve temas açısı (tedavi sıcaklığı 110°C)
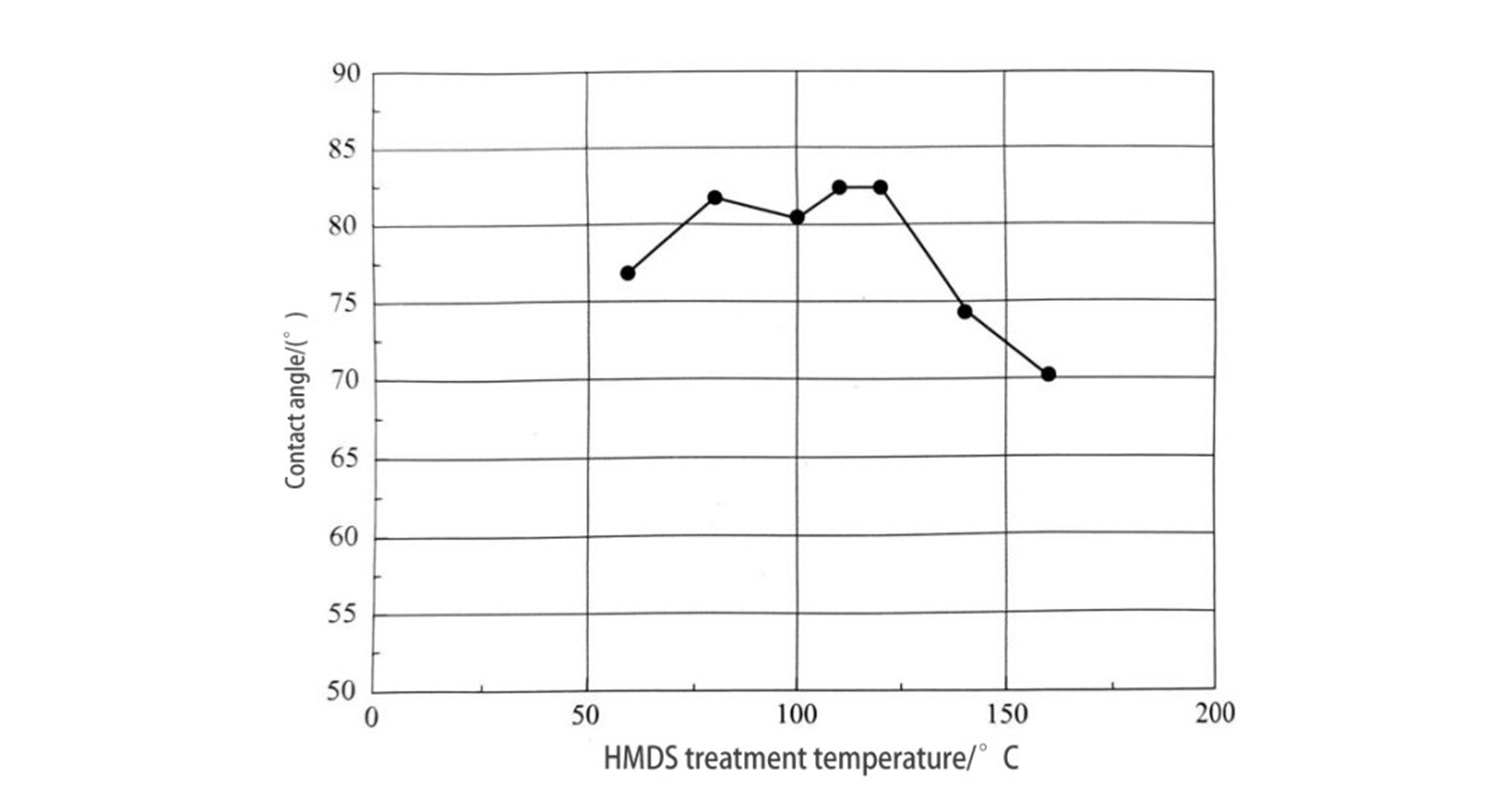
Şekil 9: HMDS işlem sıcaklığı ile temas açısı arasındaki ilişki (tedavi süresi 60 saniye)
HMDS işlemi, bir fotodirenç modeli oluşturmak için oksit filmli bir silikon substrat üzerinde gerçekleştirilir. Oksit film daha sonra bir tampon eklenerek hidroflorik asit ile kazınır ve HMDS işleminden sonra fotodirenç modelinin düşmesinin engellenebildiği bulunmuştur. Şekil 10, HMDS işleminin etkisini göstermektedir (desen boyutu 1 um'dir).
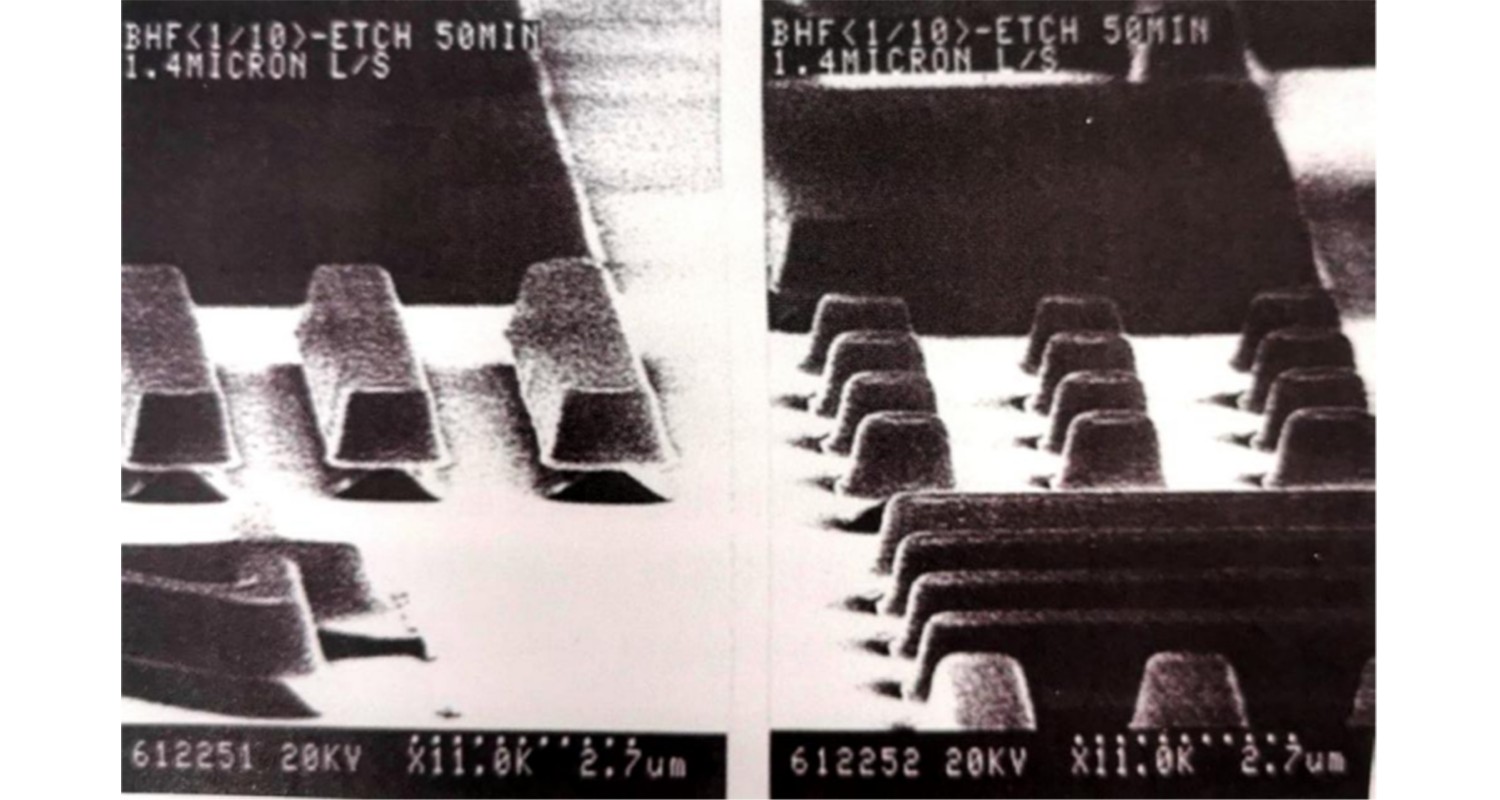
Şekil 10: HMDS işlem etkisi (desen boyutu 1um'dur)
Ön pişirme
Aynı dönme hızında, ön pişirme sıcaklığı ne kadar yüksek olursa, film kalınlığı o kadar küçük olur; bu da, ön pişirme sıcaklığı ne kadar yüksek olursa solventin o kadar fazla buharlaşacağını ve bunun da daha ince bir film kalınlığına yol açacağını gösterir. Şekil 11'de ön pişirme sıcaklığı ile Dill's A parametresi arasındaki ilişki gösterilmektedir. A parametresi ışığa duyarlı maddenin konsantrasyonunu gösterir. Şekilden görülebileceği gibi ön pişirme sıcaklığı 140°C'nin üzerine çıktığında A parametresi azalmakta, bu da ışığa duyarlı maddenin bundan daha yüksek bir sıcaklıkta bozunduğunu göstermektedir. Şekil 12, farklı ön pişirme sıcaklıklarında spektral geçirgenliği göstermektedir. 160°C ve 180°C'de 300-500nm dalga boyu aralığında geçirgenlikte bir artış gözlemlenebilir. Bu, ışığa duyarlı maddenin yüksek sıcaklıklarda pişirildiğini ve ayrıştığını doğrular. Ön pişirme sıcaklığı, ışık özellikleri ve hassasiyete göre belirlenen optimum bir değere sahiptir.
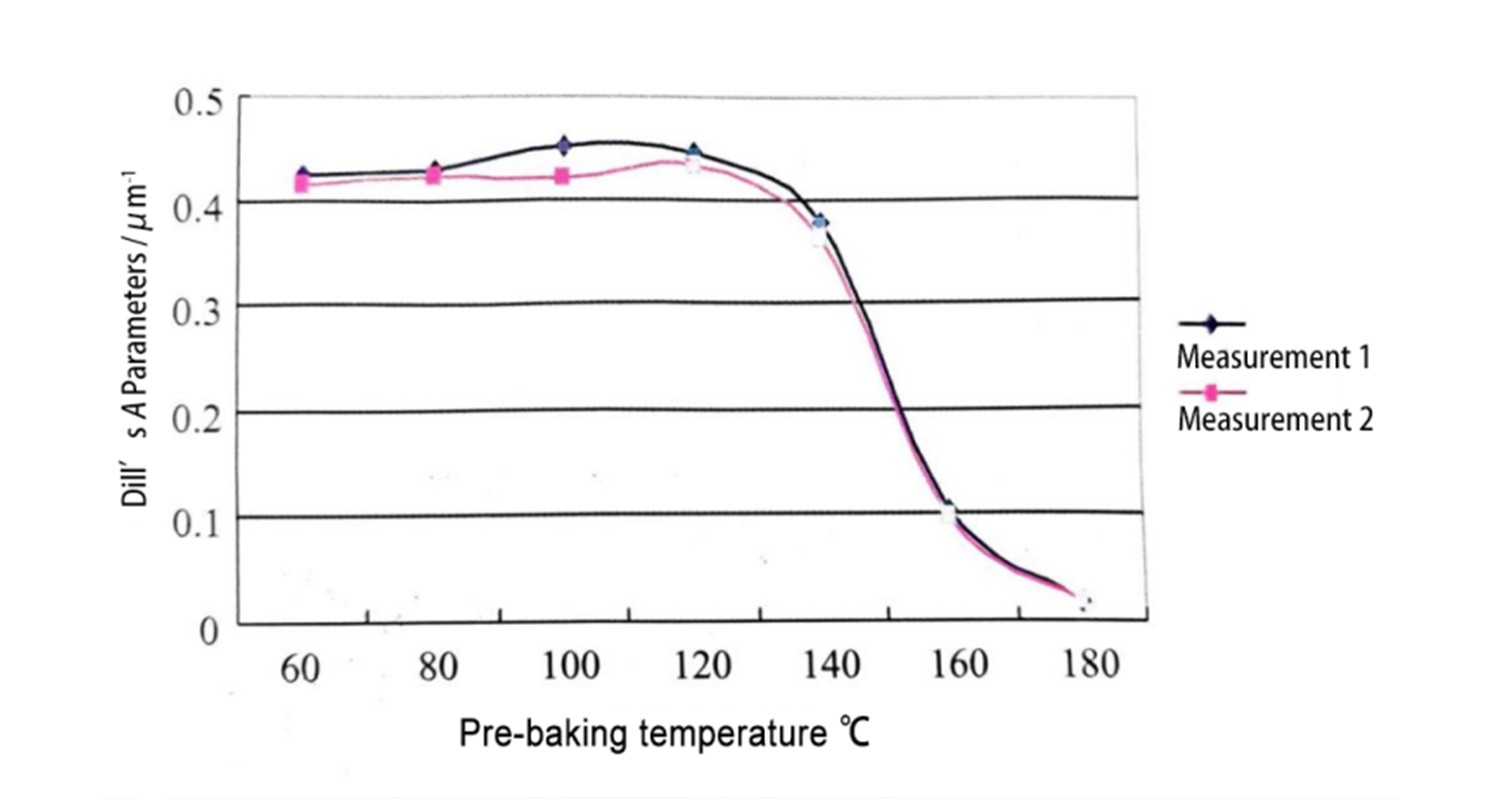
Şekil 11: Ön pişirme sıcaklığı ile Dill's A parametresi arasındaki ilişki
(OPR-800/2'nin ölçülen değeri)
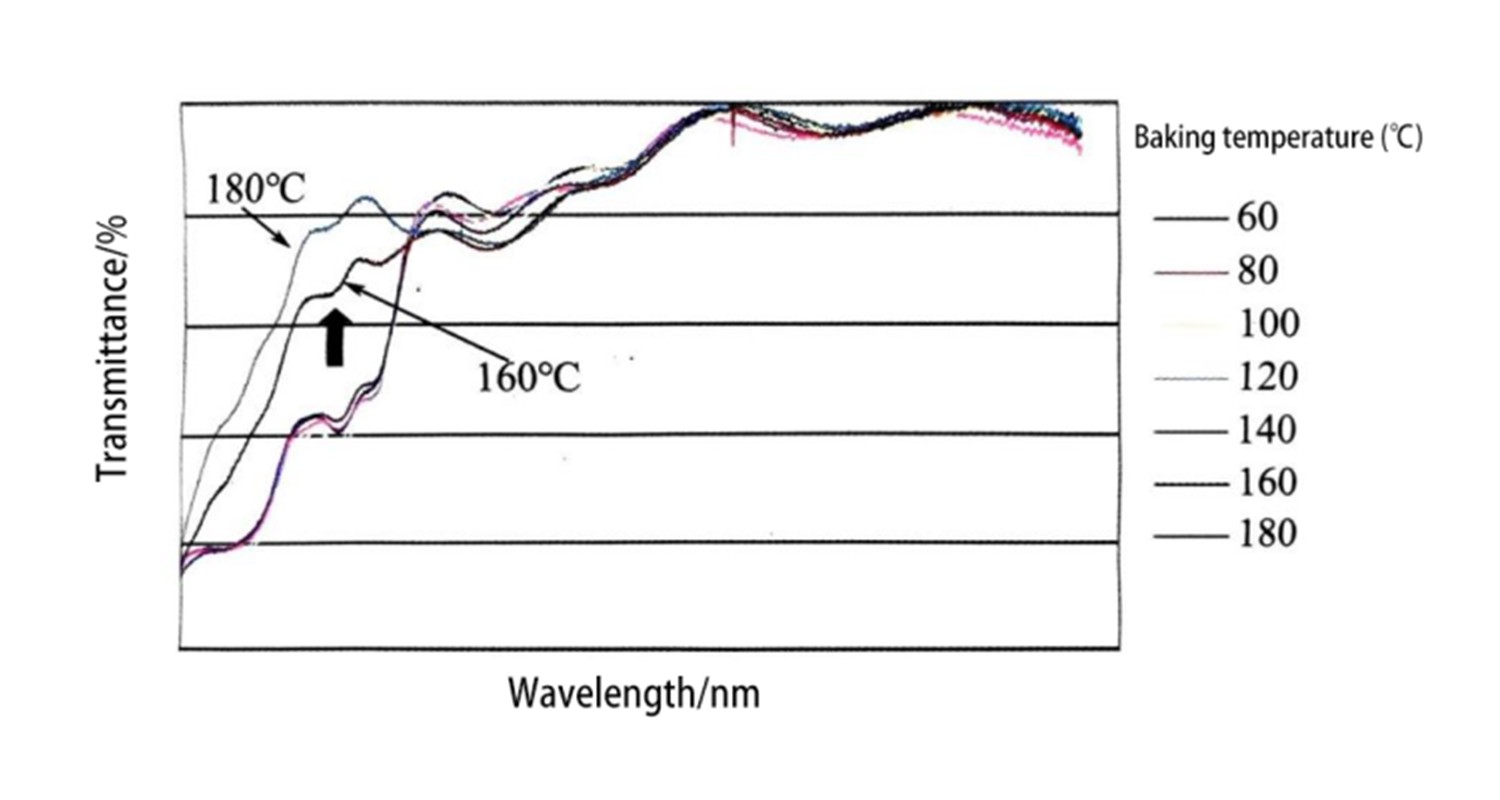
Şekil 12: Farklı ön pişirme sıcaklıklarında spektral geçirgenlik
(OFPR-800, 1um film kalınlığı)
Kısaca, döndürerek kaplama yöntemi, film kalınlığının hassas kontrolü, yüksek maliyet performansı, yumuşak işlem koşulları ve basit operasyon gibi benzersiz avantajlara sahiptir, dolayısıyla kirliliğin azaltılması, enerji tasarrufu ve maliyet performansının iyileştirilmesinde önemli etkilere sahiptir. Son yıllarda döndürerek kaplama giderek daha fazla ilgi görmekte ve uygulaması giderek çeşitli alanlara yayılmaktadır.
Gönderim zamanı: Kasım-27-2024